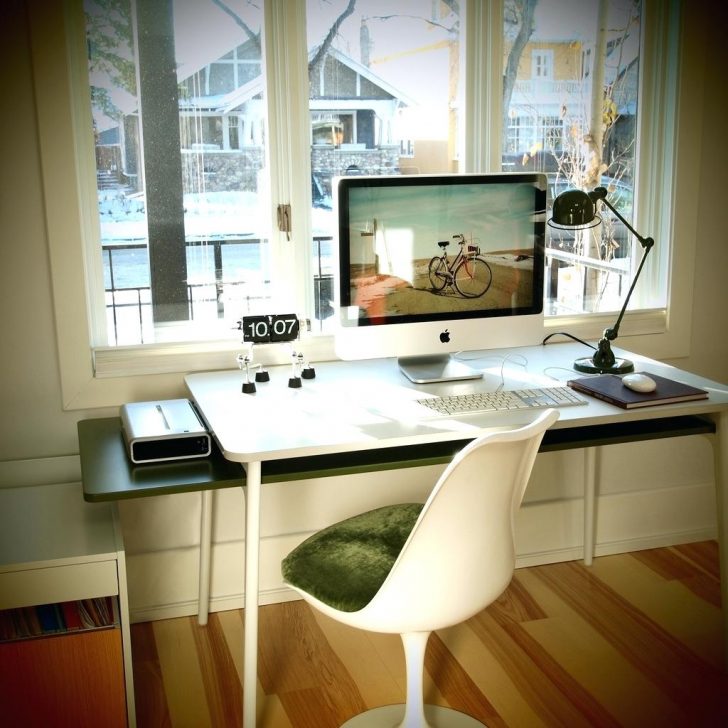
Five things nobody has told you about the Apple iMac
‘Things Nobody Has Told You…’ is my occasional column touching on tangential, but interesting, details that have been lost or under-reported in the news.
Sometimes they are ground-breakers, sometimes pieces of trivia that will enliven a dinner party conversation…
Apple has just announced the iMac Pro, a sleek, gorgeous version of the iMac, on sale now. So, this is a good moment to share some things you never knew about Apple’s desktop computers.
1 What CTO iMacs are and where they are made
Here’s a riddle to test somebody’s knowledge of Apple. Where is Apple’s only wholly-owned manufacturing facility in the world? Cupertino, you venture? Shenzhen, perhaps? No, it’s Cork, Ireland. That’s the Irish city, population 125,622, where Apple employs over 5,500 people, many working in the factory.
This is the place where Apple staff assemble the iMacs which are CTO (that’s configure-to-order), models for sale in Europe, Middle East and Africa.
There are other manufacturing facilities but these are owned by other companies.
In the corner of the wide-open expanse that is the Cork assembly-line, there is a room surrounded by metal fencing. This is where the components which make up the iMac are stored and until they leave this special area, they belong to the component maker or reseller. Only when it crosses the threshold into the main area of the factory does each element become Apple’s property. This cage contains the inventory for the next day’s manufacturing.
2 The boxes come with bits of iMac in them
You may be familiar with the distinctively shaped brown cardboard box in which Apple iMacs are shipped. These come from China. But because when you’re transporting by cargo container, you pay for size not weight, Apple takes advantage of this. Inside the brown box is the one with the picture of the iMac on, informally called the pretty box. And inside that is the iMac enclosure (that is the back of the machine), the power supply, the fan and the two speakers. It’s a clever way to maximize the efficiency of what comes in the initial shipment.
3 Detail is important
Inside the iMac is a rubber gasket, a strip of rubber in an L shape which runs up and along on the right hand side of the machine. It’s to prevent electro-magnetic interference. It’s only needed on the right-hand side. But this is Apple, so a similar gasket is placed on the other side of the rear of the enclosure, making a pleasingly symmetrical effect when you look at it.
And the level of attention to detail that this represents is magnified when you realize that this is something almost nobody will ever see, as it’s inside a sealed unit! Well, if a job’s worth doing…
It emphasizes how Apple has earned its reputation for going further than anyone else, for sanding the underside of the drawers, as it were. Look no further than the PCBs (Printed Circuit Boards). Again, this is a part most users will never see but still, Apple insists they should be black, not the industry-standard green. Similarly, the foam that comes with each iMac is one of two versions. There’s a slot where the keyboard fits and since there are two sizes of keyboard, compact and full-length, there are two different pieces of foam. Other companies might consider putting, you know, a foam block to fill up the space but no, not Apple. Instead it uses foam blocks which are designed in two different ways. If you’re interested, 70 per cent of purchase are for the short keyboard.
4 They’re quick to build, and they’re not
Watching the guys in Cork assemble an iMac is almost hypnotic. They are skilled, and very fast. In fact, the iMac is assembled in not much more than 35 minutes. But that’s not the end of the story. Every single iMac they build then goes through quality control and testing. Each is power-cycled multiple times, and run for between nine and 22 hours. If everything works perfectly, it’s on its way.
Of the assembly line products, a much smaller percentage go through even more thorough testing and if a fault is found in any of these, say a key fails on a keyboard, then the next 44 units are checked for this fault to avoid a repeating error.
In total, the Cork assembly line makes between thousands of iMacs a week. Of the staff there, 35% of the labor is involved in the assembly and packing, but 65% in quality checking and testing.
5 It all moves at quite the pace
There’s a section of the factory with walls and glass panels to keep you out. That’s because on the other side are robots who dash around at quite a pace. iMacs are clamped into place on square wooden trays. The screens are switched on and the iMacs are powered from underneath. But as one robot truck passes its load to the next, the power is transferred to metallic strips underneath the tray. The clamps holding the computers in place have to be solid because the trucks zoom back and forth faster than you would believe. It’s quite a sight, – writes Forbes.